Exemplary Tips About What Is The Difference Between EBOM And MBOM In Windchill

EBOM vs. MBOM in Windchill
1. Understanding the Core Concepts
Ever felt like you're swimming in an alphabet soup of acronyms when dealing with product lifecycle management (PLM) systems like Windchill? You're not alone! Two terms that often cause confusion are EBOM and MBOM. Let's break them down in a way that even your grandma could understand. Think of it this way: one focuses on what you're selling, and the other focuses on how you're making it. Simple, right? Let's dive a bit deeper.
EBOM stands for Engineering Bill of Materials. It's essentially a complete, structured list of all the parts, assemblies, and components needed to design and engineer a product. This is usually created by the engineering team. The EBOM is design-centric, representing the product as conceived by engineers. Think of it as the blueprint for your product. It defines what functions it will perform and what key features it will have.
On the flip side, MBOM stands for Manufacturing Bill of Materials. This represents all the parts, components, and assemblies required to manufacture a product. It's a detailed instruction manual for the production team, outlining the exact steps and materials needed to build the product. This is usually created by the manufacturing engineering team. It is process-centric, considering the manufacturing process, tools, and resources available.
The key thing to remember is that the EBOM and MBOM may not always be identical. They represent different perspectives on the same product. The EBOM is about the "what," and the MBOM is about the "how." Imagine trying to bake a cake. The EBOM is like the recipe (ingredients and instructions), while the MBOM includes details like the specific oven temperature, the size of the mixing bowl, and even which spatula to use! Sometimes you need extra details for efficient production, right?
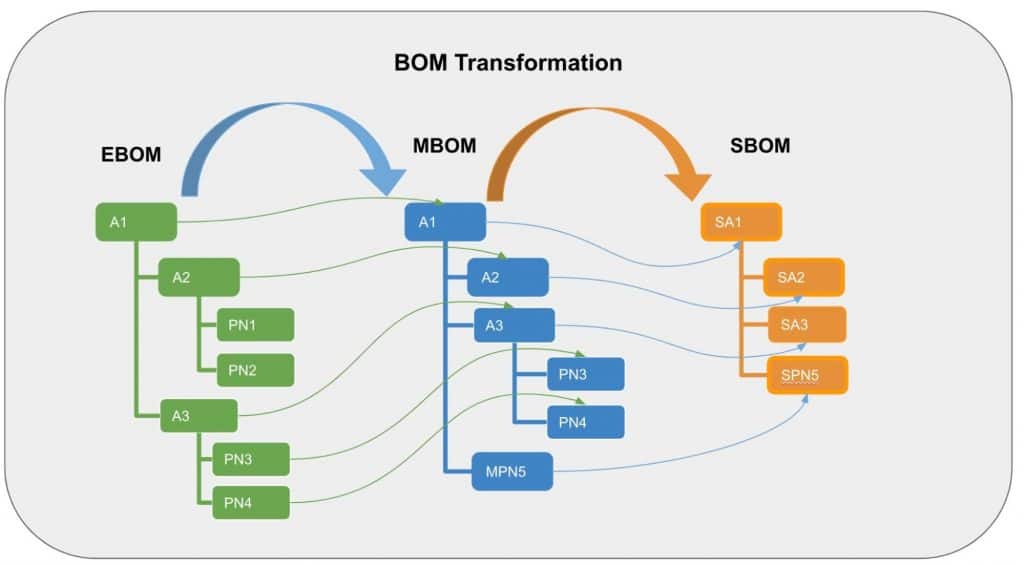
Bill Of Materials Transformation (EBOMMBOMSBOM) OpenBOM
Delving Deeper
2. Exploring the Nuances of Each BOM
So, we know the basics, but what specifically makes these two BOMs different? Let's get into the details. It's not just about different departments using them; it's about the fundamental purpose they serve.
One of the biggest differences lies in the level of detail. The MBOM usually contains more information about the manufacturing process than the EBOM. This includes things like tooling requirements, work instructions, and machine settings. For example, an EBOM might specify a type of screw, while the MBOM will tell the production team exactly which screwdriver to use and the torque settings.
Another key difference is the way the BOMs are structured. The EBOM is often organized by function or feature, reflecting the engineering design. The MBOM, on the other hand, is structured according to the manufacturing process, reflecting the sequence of operations performed on the shop floor. Think of it as building blocks versus an assembly line.
Think about paint for your product. The EBOM might just say "red paint." The MBOM, however, needs details like the specific shade of red (Pantone 185 C, maybe?), the type of paint (acrylic, enamel?), the quantity required, and even the method of application (spray, brush?). It's all about getting that perfect factory finish!

Webinar EBOM MBOM Transformatie CAD Services
Why Are Both BOMs Important in Windchill?
3. Understanding the Collaborative Power
You might be thinking, "Okay, I get the difference. But why do I need both?" Excellent question! The beauty of using both EBOMs and MBOMs in Windchill lies in their ability to foster collaboration and communication across different departments.
Having both BOMs allows for better change management. When engineering makes a change to the design, the impact on manufacturing can be immediately assessed. Conversely, if manufacturing identifies a more efficient way to build the product, the engineering team can evaluate the proposed change to ensure it doesn't compromise the design. This prevents costly rework and delays later in the product lifecycle.
Furthermore, using both BOMs supports concurrent engineering. This means that engineering and manufacturing can work simultaneously on the product design and manufacturing process. This reduces lead times and allows for faster product development. The ability to view both perspectives in a unified platform like Windchill is extremely valuable.
Imagine the chaos if these teams operated in silos! One team designing a product that's impossible to manufacture, the other team building a product that doesn't meet the required specifications. By using both EBOMs and MBOMs, you're ensuring that everyone is on the same page and working towards the same goal — a successful product!

Bridging the Gap
4. How Windchill Facilitates the Conversion
So, how do you actually go from an EBOM to an MBOM? This is where the magic of Windchill really shines. Windchill provides tools and capabilities to transform the EBOM into an MBOM, ensuring consistency and accuracy. It's not just a copy-paste operation, though. It's a carefully managed process.
Windchill allows you to associate manufacturing information with the EBOM components. This information can include things like manufacturing processes, tooling requirements, and work instructions. Once this information is associated, it can be automatically transferred to the MBOM during the transformation process. Think of it as adding extra "manufacturing attributes" to each part within your design.
One of the key features is the ability to define transformation rules. These rules specify how the EBOM should be transformed into the MBOM. For example, you can define rules to automatically add certain components or operations based on the EBOM structure. This automates the transformation process and reduces the risk of errors. It's like having a smart assistant that knows exactly how to translate your design into a manufacturing plan.
Manual adjustments are almost always required! Windchill provides tools for making manual modifications to the MBOM. This allows manufacturing engineers to fine-tune the manufacturing process to optimize efficiency and reduce costs. The process should be iterative and collaborative, with feedback flowing between engineering and manufacturing to continuously improve the product and the process. Don't be afraid to get your hands dirty and tweak things! Collaboration is key!

EBOM Vs. MBOM SBOM Key Differences & Best Practices
Real-World Benefits
5. Practical Applications of Using EBOM and MBOM
Enough theory! Let's talk about real-world benefits. What happens when you effectively manage both EBOMs and MBOMs within Windchill? The results can be significant, impacting everything from time to market to product quality.
One of the biggest benefits is reduced time to market. By streamlining the product development process and enabling concurrent engineering, you can bring products to market faster. A coordinated EBOM and MBOM allow for earlier validation of manufacturability and reduced surprises on the shop floor.
Another key benefit is improved product quality. By ensuring that the manufacturing process is aligned with the engineering design, you can reduce the risk of defects and improve the overall quality of your products. The alignment gives you confidence in your product when it hits the market.
Finally, there's the cost reduction aspect. Better collaboration, streamlined processes, and reduced errors all contribute to lower costs. Improved inventory management, reduced scrap, and more efficient use of resources also contribute to cost savings. Happy manufacturing teams are often cost-effective manufacturing teams!
FAQs
6. Addressing Common Inquiries
Still have some questions lingering in your mind? Let's tackle some frequently asked questions about EBOMs and MBOMs in Windchill.
Q: Can one part number exist in both the EBOM and the MBOM?
A: Absolutely! A single part number can absolutely exist in both. It simply signifies that the same component is used in the design and is also part of the manufacturing process. However, the information associated with that part number might differ slightly between the two BOMs.
Q: What happens if the EBOM and MBOM are not synchronized?
A: Chaos! Okay, maybe not complete chaos, but definitely problems. Misaligned BOMs can lead to manufacturing errors, delays, increased costs, and even product recalls. Maintaining synchronization is crucial for efficient product development.
Q: Is Windchill the only PLM system that uses EBOMs and MBOMs?
A: Nope! Most PLM systems use the concept of EBOMs and MBOMs, although the specific terminology or implementation might vary. The underlying principle remains the same: to manage the design and manufacturing aspects of a product.
Q: Our company is small; do we really need both EBOM and MBOM?
A: Even for smaller companies, having a clear distinction between design intent (EBOM) and manufacturing execution (MBOM) is beneficial. While you might not need all the advanced features of Windchill, the concept of managing these two perspectives separately can still improve efficiency and reduce errors.